We all know that plastic products usually have a shrinkage rate, and it shrinks when it becomes lower. Products made from different materials have different shrinkage rates. Here, we discuss several factors influencing the shrinkage of plastic turnover bins during the production phase. In fact, in production, if you want the product size to be more appropriate, it is helpful to understand the factors affecting the contraction. After all, in the industrial logistics industry, plastic turnover containers are generally standardized standardized containers. Its size and specifications are relatively accurate according to the standard, and there is no deviation. Otherwise, it cannot be said that the generalization is standardized.
The molding process of the plastic turnover box is the thermoplastic molding. Due to the volume change during the production process in the crystallization process, the internal stress is relatively large, and there is a residual stress within the mold product, and the molecular orientation is very strong. Therefore, it has a higher shrinkage rate than the thermosetting plastics products. It has a larger contraction range and a very pronounced directionality. Since the outer layer of the molten material is in contact with the mold cavity surface during the molded plastic component, it is immediately cooled down to form a low-density solid shell. And we all know that the thermal conductivity of plastic is very poor, and the inner layer of the plastic turnover box cools very slowly, forming a high-density solid layer with a large shrinkage rate. If the wall thickness is slow, the high-density layer will thicken and will shrink more.
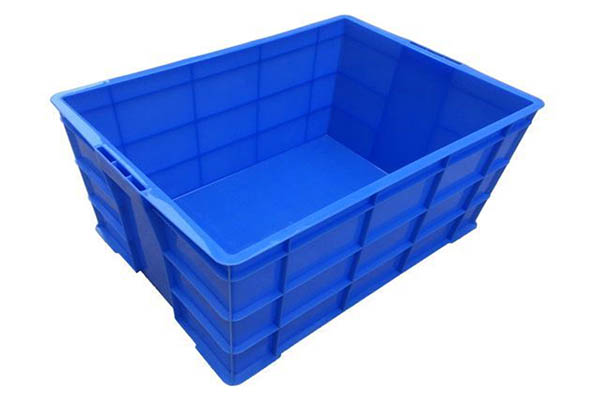
The molding process of the plastic turnover box is the thermoplastic molding. Due to the volume change during the production process in the crystallization process, the internal stress is relatively large, and there is a residual stress within the mold product, and the molecular orientation is very strong. Therefore, it has a higher shrinkage rate than the thermosetting plastics products. It has a larger contraction range and a very pronounced directionality. Since the outer layer of the molten material is in contact with the mold cavity surface during the molded plastic component, it is immediately cooled down to form a low-density solid shell. And we all know that the thermal conductivity of plastic is very poor, and the inner layer of the plastic turnover box cools very slowly, forming a high-density solid layer with a large shrinkage rate. If the wall thickness is slow, the high-density layer will thicken and will shrink more.
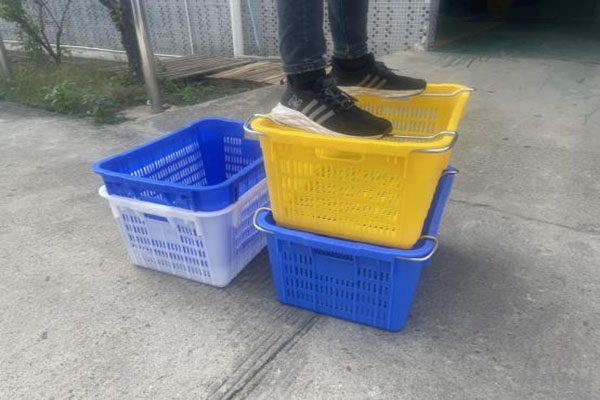
Feed port form of production equipment'size raw material distribution and other factors will directly affect the flow direction, product material density distribution, pressure protection contraction and molding time, indirectly affect the shrinkage rate of plastic turnover box. When the equipment has a direct inlet, the inlet cross section is very large, especially when it is thicker, the shrinkage rate will be smaller but more directional. In contrast, when the inlet size is small, the contraction direction is small, and the shrinkage rate is relatively large when the inlet is relatively close to the inlet or parallel to the flow direction.

Production molding conditions have a great influence on the shrinkage rate of plastic turnover box. For example, if the mold temperature is high and the molten material ols slowly, there is a high density and the shrinkage rate will be relatively large. The crystalline material has high crystallinity and large volume, so the shrinkage rate becomes larger. The mold temperature distribution and the internal and external cooling degree and density uniformity of plastic components will directly affect the shrinkage rate and directionality of each part of the product. The size of the retention pressure and the length of the retention time also have a great impact on the contraction rate. When the pressure is high and long, the contraction rate is smaller, but the direction is greater. During the molding process, the shrinkage rate of the plastic turnover box can be appropriately changed by adjusting the mold temperature and pressure injection speed and cooling time. According to the above, we can determine the shrinkage rate of each part of the product according to the plastic turnover box shrinkage wall thickness shape feed inlet shape and size and the distribution of the mold design, and then calculate the cavity.size. According to the actual shrinkage rate of the product, change the mold and change the injection molding conditions to correct the product shrinkage rate to meet the actual requirements.
Post time: Nov-25-2022