Flexographic pallet, that is, flexographic printing pallet, which has unique flexibility, economy, and is beneficial to the protection of the environment, has made great progress in the application of pallet packaging in China in recent years. This paper reviews and summarizes the common failure causes and solutions in flexographic printing.
Wrinkling, paper deposition and plate blocking are common faults in flexo printing process, which will seriously affect the normal production. The following three kinds of fault causes and troubleshooting methods are introduced respectively.
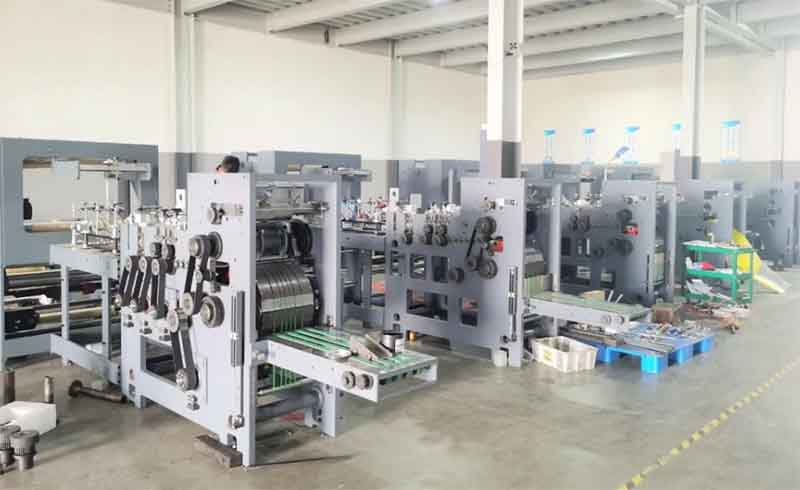
Picture wrinkle - cause of failure and solution
① Excessive local tension. For example, if the uncoiling tension is set too large, the solution is to reduce the set value of the tension of each part and use a special printer pallet to carry paper.
② The device does not match the printing material. The solution is to consult the flexo printing mechanism manufacturer, and timely replace a set of embossing rollers suitable for printing thin paper and the nonstop pallet for paper feed and paper output, so as to meet the printing material requirements.
③ The Angle of deviation correction device is too large. This phenomenon occurs in the printing stage, because the Angle of the correction device is too large and the tightness on both sides of the paper is inconsistent, and the looser side is easy to wrinkle. The solution is to fix the paper in the slotted top pallet, and the system introduces a fully automated paper feeding pallet
④ Flexographic printing using light pressure printing, printing pressure adjustment and standard pallet packaging is one of the key factors affecting the quality of flexographic printing.
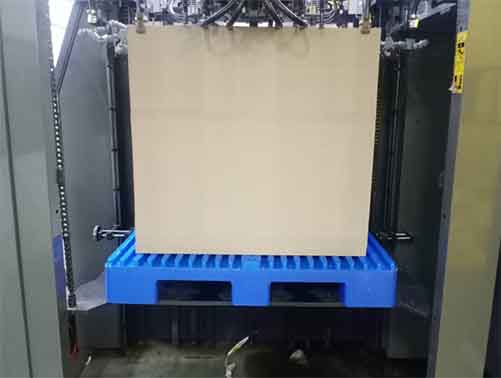
Compared with offset printing, flexible printing plates have a certain degree of elasticity, and the proportion of dot increase generated in the printing process is larger, about 15%, sometimes as high as 20%. The intermediate adjustment area of about 40% of the dot is close to the critical point of 70% of the flexographic printing dot after the increase of the dot, the probability of the dot overlap is high, and the adjacent dot will stick, resulting in the blocking failure. Therefore, through pre-press compensation, try to classify the paper products with different printer pallets, distinguish them, and facilitate operation with plastic pallet.
The printing pallet and packaging pallet can assist the operator to correctly adjust the pressure at both ends of the embossing cylinder and the plate cylinder, the inking pressure,
And ink transfer pressure and imprint pressure, so that the size of the two remain consistent, circular horizontal contact; In the printing process, it is adjusted at any time according to the specific situation of printing to keep it in the best state, which is of great significance to improve the quality of flexo printing.
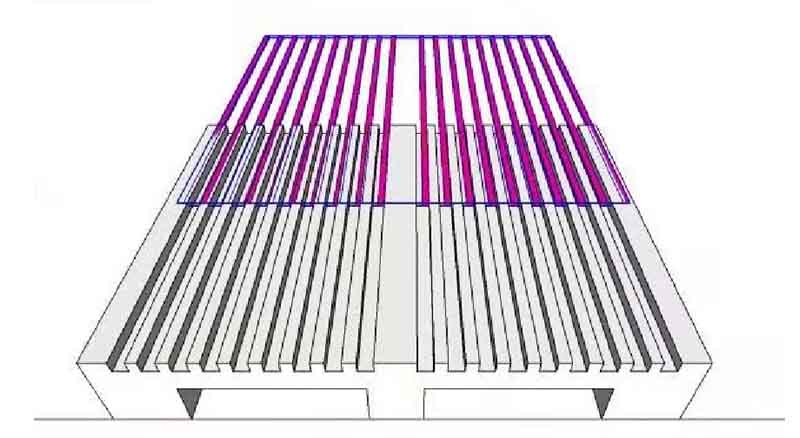
Post time: Sep-20-2023